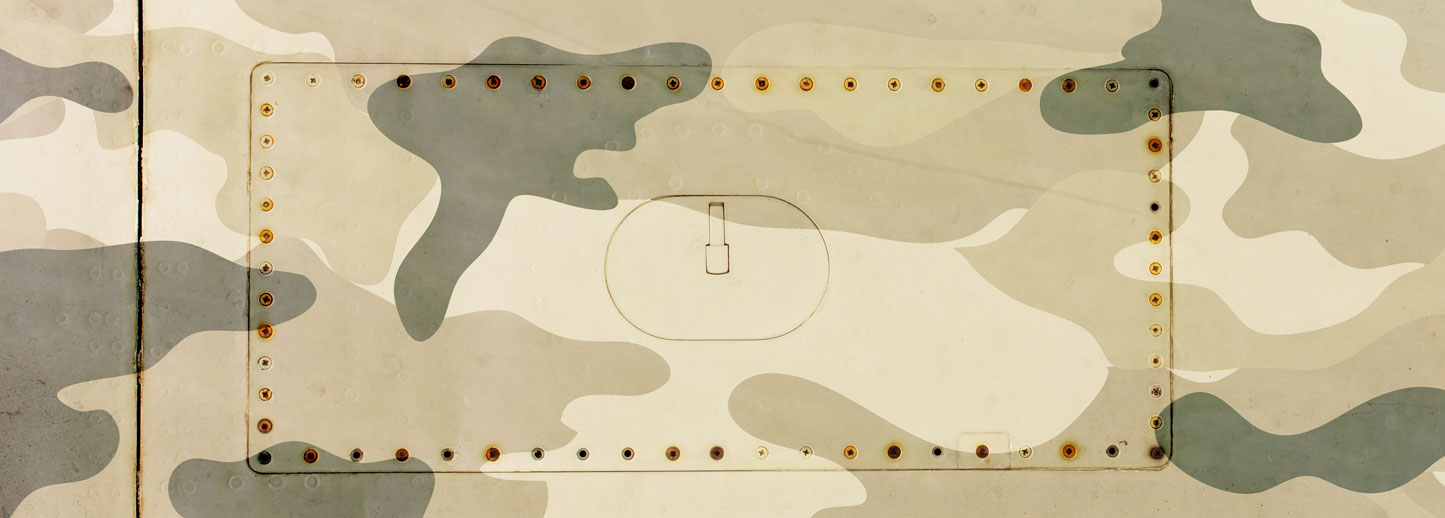
Clear Water Rinse Systems Mitigate Risk and Reduce Maintenance Costs
SITUATION: Corrosion – the natural deterioration of metal when it reacts with various environmental conditions – is a costly, hazardous problem that affects every sector of the economy, including consumer products, utilities, construction, and transportation. It is a particular challenge in commercial and military aviation, where corrosion compromises safety and performance, erodes productivity, and adds significantly to the cost of aircraft maintenance.
Corrosion can render an aircraft un-airworthy by weakening structural components, roughening the outer surface, loosening fasteners, hastening cracking, and facilitating the entry of water into electronic fixtures. Left untreated, corrosion can hasten other conditions that will eventually cause structural failure. Corrosion can quickly develop in key areas, where loss of even a small degree of material integrity
can allow moisture, salt, sand, and other contaminants to enter, sometimes with catastrophic results. The crash of an El-Al Boeing 747 in Amsterdam (1992), the crash of a China Airlines Boeing 747-200F (1991), and the incident in 1988 in which a hole was torn in the fuselage of an Aloha Boeing 737 as it flew over Hawaii were all traced to structural damage caused by corrosion.
Corrosion can affect entire fleets of aircrafts, causing delays and compromising military readiness:
- The crash of a 28-year-old F-15C Eagle fighter in Virginia in 2014 and the break-up of another F15-C over Missouri in 2007 focused attention on the aging of the U.S. Air Force’s fleet of fighters, bombers, and tanker aircrafts. Concerns about metal fatigue and corrosion forced the grounding of the entire F-15 fleet during the investigation of the 2014 incident, and prompted placing F-15Es on ground alert while flying missions in Iraq and Afghanistan with other aircrafts.
- Nearly one of every five of the Marine Corps’ aircraft – as many as 134 aircrafts, including F/A-18 Hornets, CH-53E Super Stallions, AV-8B Harriers, MV-22B Ospreys, and H-1 Hueys – were grounded in early 2015 due to high levels of corrosion.
- Over many years, problems with the cabin pressurization system in the U.S. Air Force’s C-130 aircraft had severely sickened pilots and crews and grounded many of the aircraft, causing costly delays. The problem was eventually traced to corrosion of a critical part.
Aircrafts are particularly vulnerable because they are constructed from a variety of metals that are subject to different types of corrosion, and because they are constantly exposed to corrosive environmental conditions.
Other factors – including the age of the plane, where it is operated, how often it is cleaned, and whether it is hangared – will also affect how quickly and to what extent corrosion will develop.
Environmental Factors
Corrosion occurs when a metal forms a chemical reaction with its environment, resulting in the oxidation, and eventual breakdown, of the metal. In aviation operations, both on the ground and in the air, specific environmental factors and the presence of certain substances make conditions right for corrosion to develop.
Atmospheric and environment conditions are the primary cause of corrosion, and they hasten the process once it has begun. Moist, oxygen-rich air, especially if it carries salts from ocean waters, is particularly damaging to metal components. Wind-borne sands and dusts are very corrosive, particularly in desert regions, where sand often carries salt from ancient oceans that once covered the arid lands. Industrial air pollution is highly corrosive. Volcanic ash is highly corrosive. The corrosion process is accelerated in hot environments.
Other substances that contribute to this corrosive mix include industrial fluids and cleaning solutions, oils and fuels, battery acid,
engine exhaust particulates, and even acidic residues from leaking galleys or lavatories.
In its Technical Manual: Cleaning and Corrosion Control, the Naval Air Systems Command explains how corrosion can damage aircraft: “High strength steels used in landing gear and launch/ recovery systems are sensitive to pitting and stress corrosion cracking, which can lead to catastrophic failure. Aluminum alloys susceptible to exfoliation and intergranular corrosion are commonly found on wing skin and other load carrying structures. Even magnesium, one of the most corrosion sensitive metals known, is still used in canopy frames and gear boxes. Added to this is the ever increasing age of military aircrafts and the need to comply with stricter environmental regulations. All of these factors combine to make corrosion prevention and control a significant factor in the safe and economic operation of military aircrafts.”
Aging Aircraft are at Special Risk
The age of the aircraft is also a significant factor. In recent years, progress has been made in the fight against corrosion, with the development of better corrosion-resistant base materials, protective surface treatments, and coatings and the introduction of corrosion prevention measures into aerospace engineering and manufacturing processes.
But older aircrafts – particularly those beyond their 20-year design life – are particularly vulnerable to corrosion, not only because they lack the newer anti-corrosive protections, but because of their total exposure over years and
decades to the harsh environments and conditions that hasten the advance of corrosion. Even under ideal conditions, all aircrafts will experience some corrosion, but as an aircraft ages, corrosion is more likely to develop, and to be more extensive.
About one quarter of all the commercial aircraft currently in operation are more than 20 years old, and the average age of planes in the United States Air Force is 24 years.
The Cost of Corrosion
Corrosion imposes a tremendous burden on aviation operations, in both direct and indirect costs.
Direct costs include:
- Special cleaning and corrosion control activities
- Inspection and maintenance
- Repair or replacement of corroded components
Indirect costs include:
- Loss of productivity due to delays, failures, etc.
- Taxes and related overhead on corrosion-related maintenance and other activities
- Litigation, fines, and loss of public good will after accidents and crashes
The U.S. military, which is deeply affected by corrosion in aviation operations, has made careful study of every aspect of the issue, including costs. Among the findings of various studies conducted by or for the U.S. military are the following:
- The Department of Defense spends more than $23 billion each year to control corrosion on aircraft and other equipment in its operations around the world. One source estimates this to be 20.5% of total maintenance costs for infrastructure, facilities, and weaponry.
- The U.S. Army’s Aviation and Missile Command spends $1.6 billion each year to address corrosion on helicopters.
- Naval Air Systems Command (NAVAIR) reports that corrosion accounts for half of all aircraft depot maintenance costs.
- Over FY2009-FY2013, corrosion-related costs for the U.S. Coast Guard were $344 million, or more than 22% of the Guard’s total maintenance budget.
- The House Armed Services Committee reports that about $7 billion of corrosion cost is preventable.
Corrosion also affects productivity, as demonstrated in studies done by or for the U.S. military:
- In 2010-2011, the average number of days per aircraft that were unavailable due to corrosion was 15.9 days for Air Force aviation, 17.4 days for Army aviation, and 26.5 days for Navy and Marine Corps aviation.
- In a similar study from FY2012, corrosion was found to be a contributing factor in 18.1% of total non-availability time for Army aviation assets, an average of 472 hours, OR 19.7 days per year per unit.
- Naval Air Systems Command (NAVAIR) estimates for each aircraft, corrosion-related activities require 350-400 person hours of labor (labor hours) and result in 9-10 weeks of unavailability per year.
First Line of Defense: Cleanliness
Aircraft designers and manufacturers have made significant improvements in the corrosion-resistance of modern aircraft. On the ground, airport and military managers are paying closer attention to corrosion, and have implemented more frequent inspections and better cleaning and maintenance.
Despite these improvements, corrosion remains a significant challenge for commercial and military aviation, requiring constant vigilance and continuous preventive maintenance.
The most effective means of preventing and mitigating corrosion is to keep aircraft clean – in particular, by removing corrosive contaminants that accumulate on the exterior of the aircraft during flight. And cleaning offers other benefits, including:
- Reducing drag and overall weight, thus improving fuel efficiency
- Facilitating inspections, done more easily on a clean aircraft
- Maintaining the plane’s appearance
The frequency and intensity of cleaning operations are largely determined by the operating environment. Aircraft operated in hot, humid areas, within ten miles of sea coasts, or in deserts, or in areas where industrial air pollution is present, or those that are not hangared, will require more frequent cleanings than aircraft operated in dry, pollution-free environments that are protected from the elements between flights.
In its Technical Manual: Cleaning and Corrosion Control, the Naval Air Systems Command (NAVAIR) specifies these cleaning schedules for its aircraft:
- In the absence of aircraft specific requirements, Navy aircraft shall be cleaned at least every 7 days when aboard ship and at least every 14 days when ashore.
- Under certain conditions, depending on the type of aircraft and usage, the normal wash cycle may not be sufficient. More frequent cleaning may be required for certain types of aircraft when exposure to salt spray, salt water, or other corrosive materials occurs.
- When deployed within three miles of salt water or when flown below 3000 feet over salt water, daily cleaning or wipe down is required on all exposed, unpainted surfaces, such as landing gear struts and actuating rods of hydraulic cylinders.
And for Army aircraft:
- The frequency of cleaning of army aircraft shall be 30 days … unless aircraft are stationed within two miles of salt water [when more frequent cleaning is required].
- Extended or low level operations over salt water require daily fresh water rinsing.
The Air Force mandates the following intervals for thorough aircraft washing, dependent on the degree of harshness of the operating environment:
- Mild: every 180 days
- Moderate: every 90 days
- Severe: every 30 days
A Practical Approach: Automated Fresh-water Rinsing
Though rinsing can be accomplished manually with hand-held hoses or other spray equipment, military regulations recommend the use of taxi-through fresh-water rinsing facilities, by which rinsing of the entire aircraft can be accomplished more effectively and far more quickly than by manual methods. The military further recommends that automatic, taxi-through rinse facilities, which use multiple jets to reach every part of the aircraft exterior, including parts difficult to reach with manual rinsing, “should be used as frequently as possible.”
Automated fresh-water rinsing facilities are a valuable supplement to cleaning operations, and offer many advantages over hand-rinsing operations, including:
- Speed – While it can take several people many hours to (RINSE) wash an aircraft, an automated rinse facility can rinse an entire fleet at under five minutes per plane.
- Effectiveness – While rinsing cannot replace washing, rinsing removes most of the salts and corrosive residues that build up between scheduled washes, thus reducing the time and effort needed for cleaning, an essential factor in large fleet operations.
- Safety – During manual rinsing procedures, workers must climb on and around aircraft, carrying unwieldy equipment and hoses, and risking slips and falls on wet surfaces. Taxi-through rinsing systems can be operated remotely, thereby reducing the risk of worker injury.
- Efficiency – Automated rinsing facilities capture, re-cycle, filter, and re-use rinse water. This is an efficient, cost-effective, environmentally-friendly approach for any facility, and an especially important consideration in desert environments.
Resources Consulted
“Aircraft Cleaning and Corrosion Control.” Chapter 6 of Aviation Maintenance Technician Handbook—General. Oklahoma City, OK: U.S. Department of Transportation, Federal Aviation Administration, Airmen Testing Standards Branch, 2008.
Aircraft Corrosion. (White Paper) NACE International (formerly National Association of Corrosion Engineers), n.d.
Aircraft Corrosion. Aircraft Owners and Pilots Association, n.d.
Read More
Albon, Courtney. “Corrosion Exec: USAF Seeing Early CPC Progress, Cost Savings Unknown.”
InsideDefense.com, July 5, 2013.
Banis, David, et al. “Design for Corrosion Control.” Aero Magazine, no. 7. Seattle, WA: Boeing Commercial Airplanes Group, 1999.
Read More
Billion-Dollar Weather and Climate Disasters: Table of Events. National Oceanic and Atmospheric Administration, National Centers for Environmental Information, 2015.
Read More
Corrosion Control for Aircraft. Federal Aviation Administration Advisory Circular AC43-4A, July 25, 1991.
Read More
“Corrosion Costs and Preventive Strategies in the United States.” Federal Highway Administration, NACE, and CC Technologies Laboratories, Inc., 2002. (FHWA-RD-01-156)
Hawkins, Kari. “Rinse facility designed to combat natural enemy. The Official Home Page of the U.S. Army, June 13, 2012
Read More
Herzberg, Eric F., et al. The Annual Cost of Corrosion for Coast Guard Aviation and Vessels. LMI, March, 2015.
Herzberg, Eric. “Corrosion Office Updates its 2009 Report on the Cost of Corrosion Within DoD; New Report Updates Data through Fiscal Year 2013.” CorrDefense, a publication of NACE International (formerly National Association of Corrosion Engineers), Winter 2014.
Herzberg, Eric. “DoD Releases New Report on the Effect of Corrosion on the Cost and Availability of Army Aviation and Missile Systems.” CorrDefense, a publication of NACE International (formerly National Association of Corrosion Engineers), November 15, 2014.
Herzberg, Eric. Impact of Corrosion on Cost and Availability to DoD. Corrosion Prevention and Control Integrated Product Team, Maintenance Symposium, November 14, 2012.
Read More
“Keeping clean.” Ground Handling International, February 2015, 52-53.
Read More
Muller, Wesley. “Keesler Technicians Solve Years-Old Mystery Illness Aboard C-130s.” Sun Herald (Biloxi, MS), April 13, s015, reprinted in Military.com
Read More
Rose, Alan, and Keith Legg. “Predicting Corrosion in Military Aircraft. Materials Performance, February 2014.
Sisk, Richard. “F-15 Crash Raises Concerns on Aging Fleet.” DoDBuzz, September 11th, 2014.
Read More
Smith, Everett J., and Scott A. Jones. “Preventing Aircraft Corrosion.” Service News (29)1: 6-16, 2005.
Lockheed Martin Corporation, Lockheed Martin Air Mobility Support
Stewart, Joshua. “3-star: 20 percent of all Marine aircraft are grounded.” Marine Corps Times, March 26, 2015.
Read More
Technical Manual: Cleaning and Corrosion Prevention and Control, Aerospace and Non-Aerospace Equipment. (F42620-00-D-0038, FA8501-07-F-A080) This manual incorporates Interim Operational Supplement (IOS) TO 1-1-691S-1, dated 25 September 2014. Secretary of the Air Force, 2014.
Technical Manual: Cleaning and Corrosion Control, Volume II: Aircraft. Naval Air Systems Command, April 2009, March 2010. NAVAIR 01-1A-509-2, TM 1-1500-344-23-2.